Tompkins Robotics: Defining Innovative Techniques of Automation
The 10 Most Innovative Companies to Watch in 2021
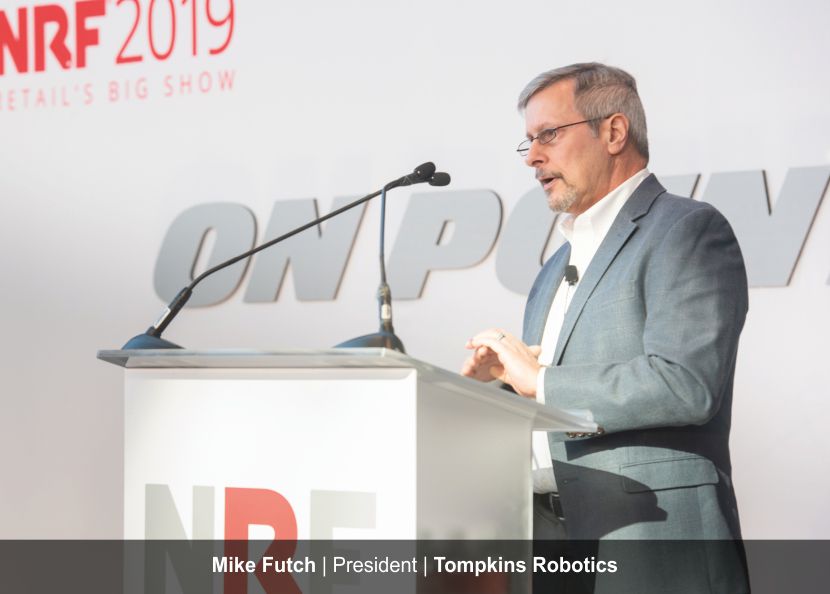
Automation in distribution centers (DC), fulfillment centers
(FC) and warehouses is not only becoming more and more important, it is
becoming a necessity. Automation adoption has continued to rise over the past
six years, as companies are facing increased pressure to cut costs, address the
workforce shortage and provide an optimal customer experience. Robotics are a
popular form of automation due to their versatility, affordability and
efficiency. Their applications span across the entire supply chain, from pick
and pack to sortation and transport. Robotic solutions also offer scalability
and rapid deployment, with a typical installation going live within just four
to six months.
In 2017, global supply chain consulting and solutions firm,
Tompkins International, launched Tompkins Robotics to
introduce an innovative material handling sortation system. A business unit of
Tompkins International, Tompkins Robotics is a leading provider of autonomous
mobile robot (AMR) solutions. The company has developed and deployed the
world’s first, portable automated sortation system, t-Sort, a revolutionary
unit and parcel sortation system that is patented for North America and Europe.
This new and innovative robotic technology helps build world-class supply
chains while providing unmatched flexibility and throughput. Tompkins Robotics’
systems accomplish volumes ranging from small operations in the backroom of a
supercenter or mall anchor store to large fulfillment centers processing
millions of units a day.
With two models, t-Sort and t-Sort Plus, and two sortation
methods, tilt trays and cross belts, Tompkins Robotics’ systems can handle
items as small as a penny to up to 40 inches long by 30 inches wide and
weighing up to 120 pounds. The fast, efficient and modular unit and parcel
sortation systems can handle a wide variety of product unmatched by traditional
sortation solutions. Given the unique flexibility and scalability of this
application, t-Sort installations have proliferated since its first
implementation in 2018 and continue to rapidly grow year over year.
t-Sort is a game-changing unit and parcel sortation system
that performs much like a tilt tray or crossbelt sorter without a fixed track,
allowing independent robots to travel freely to any divert or induction station
along the shortest path, greatly enhancing efficiency and maximizing
operational capabilities. Unlike traditional sortation systems that require a
large upfront investment and have excess capacity that may be underutilized for
years, the t-Sort system is fully modular and allows robots, chutes or
induction stations to be added or removed instantaneously without any
interruption or downtime. A typical installation takes six months or less to go
live, and the completely portable system can be collapsed or set up in minutes
and relocated to another location overnight, providing an added level of
versatility.
Other major benefits of the t-Sort solution include:
- Maximum
Efficiency: Robot navigation via real-time control to ensure movement
along the most efficient path.
- Space-Saving:
Utilizes approximately 25 percent of the space of traditional sorters.
- Wide
Range: Multiple interchangeable tray designs are capable of handling a
wide variety of products for any size or type of operations.
- Rapid
Implementation: Installation time is less than half of that of
traditional tilt tray and cross belt sorters.
- Cost-Saving:
Investment is between one third and one half of the cost of traditional
sortation systems and generates more than twice the ROI.
- High
Volume and Capacity: A single t-Sort system can handle 50,000 units
per day per module and between 5-6 million annual units.
- Labor
Productivity – High sort density in compact space results in
larger batches for greater picking efficiency and productivity.
- Redundancy
& Risk Mitigation – No single point of failure anywhere in
the system. The system has mirrored servers, redundant infrastructure and
an uninterruptable power supply backup.
The t-Sort system is powered by the Tompkins Warehouse
Execution System (tWES), which eases the implementation through its quickly
configurable design and is highly flexible with the ability to interface with a
variety of host systems.
t-Sort, combined with tWES, helps further evolve supply
chain automation, improving the efficiency of logistics operations. t-Sort is a
highly effective solution for automated order fulfillment with the flexibility
to sort both units to complete an order and parcels for shipping operations.
The system’s unique flexibility and wide range of capabilities improve the flow
of goods, labor productivity, operations planning, implementation, space
utilization, use of capital and operating expenses, and ultimately, customer
service.
Tompkins
Robotics’ award-winning t-Sort system is used by some of the world’s
top retailers and shippers, which together represent more than $1 trillion in
annual revenue and include retail, e-commerce, 3PL, and package and postal
channels. The company also integrates with key partners to grow its overall
offering on its goal of providing dock to dock robotic automation in logistics
facilities.
The t-Sort system’s unique design provides unheard of
flexibility and enables a tremendous reduction in capital cost and space in the
warehouse, compared to traditional automated sortation systems. t-Sort users
experience lower and delayed investment, shorter lead times, faster
implementation, reduced space and labor, and greater ROI.